UConn Formula SAE
UConn Formula SAE is a group of collegiate students who - over the course of a year - design, build, and compete with a formula style car. The UConn team is one of the highest performing teams around the world, boasting a 4th overall finish at the international competition at the Michigan International Speedway, competing in a pool of 120 teams. Other notable accomplishments include 2nd overall at the Pittsburgh Shootout, 1st overall at the CART Autocross at Mohegan Sun, 5th in Autocross in Michigan, and 6th in Endurance in Michigan.
​
I joined the UConn Formula SAE team when I was a a freshman, working primarily within the suspension subsystem. I ran for the position of Suspension Lead for my sophomore year, ultimately losing to a more experienced member. However, I continued to be dedicated to the club and system and was given my first major design project - the Upright
​​
The Upright
​
The Upright is a suspension component that acts as the connection between the hub/spindle combined part (internally referred to as the hindle), and the linkages that connect the suspension to the frame of the vehicle.
​
I began by researching previous designs by the team and asking previous designers about their choices. In these discussions, along with those with other members of the current team, I felt I had a good handle on the project. I then decided to put down absolutely everything I could relating to the part - interfaces, materials, forces, team goals and more. A master list of answers to "What does it do? Why does it do it? How does it do it?" This was the first time I had designed something start to finish, and I have learned that this early process is integral
​
Once I knew the answers to those questions, I began the design phase in SolidWorks. I started with extremely basic geometry sketches. Thankfully, the suspension geometry had been decided already, so I was able to build around defined point of contact.
While dealing with this design, I was doing other decision making in parallel. A decision matrix, sometimes called a Pugh chart, was used to decide the material that would be used. Titanium was chosen, as the team had recently acquired a sponsorship from a company willing to provide a six of these parts, using their titanium sintering process, for no cost.
​
After the initial design phase, I imported the part to Ansys, simulating the forces the part will see and making the proper part adjustments. Due to the capabilities of titanium sintering, I used topographic optimization to observe where material could be eliminated. After many iterations of the part were put through Ansys simulations, and interfacing checks with all related parts, a finished design was decided on.
​
Unfortunately, this design never saw the finished vehicle. Due to administrative changes within the sponsoring company, they were unable to complete the manufacturing. This left the team in a time crunch - with about two weeks to complete a new design, compatible with a 5-axis CNC machine, and withstanding the forces with the part now being made out of aluminum.
​
With the assistance of a UConn FSAE alum, and current Mastercam employee, a new design was completed and refined using the same process, within the time constraints. The part still met the weight and strength goal, actually being significantly lighter than previous uprights. This project remains the one I am most proud of.

Figure 1: Completed UConn FSAE Vehicle for 2022-2023, the CT14

Figure 2: Material Selection for the CT14 Upright

Figure 3: The results of an early topographic optimization of the upright in Ansys

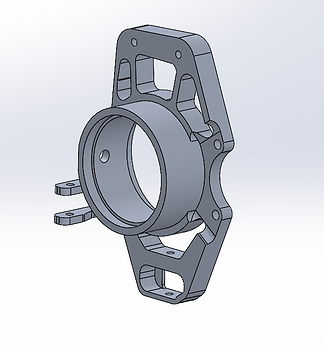

Figure 4: Final design of the CT14 upright, to be made with Aluminum

Figure 5: Drawing of the CT14 full corner assembly